Category Archive: Product Spotlight
GRAVITROL® Extrusion Control Systems: The Complete System
This week Process Control Corporation is pleased to spotlight its GRAVITROL® Extrusion Control Systems. Gravitrol® extrusion control offers the benefits of improved product quality, reduced material usage, quicker startups and product changeovers, reduced scrap, and improved product repeatability. At the same time, it reduces the operator’s workload by maintaining a constant output, regardless of screen pack or material variations.
The system uses Process Control’s proven Gravitrol® software to automate the control of the line and hold the extruder output to +/- 0.5% by weight. This tight control of output means that product can be made consistently within tolerance at the lowest possible cost, thereby saving thousands of dollars in resin.
Process Control X Series blenders can be equipped with extrusion control software to allow the blender to control the extruder and line speed on monoextrusion lines for consistent output by weight. Guardian® batch blenders can also be equipped with weigh hopper and extruder and line speed I/O.
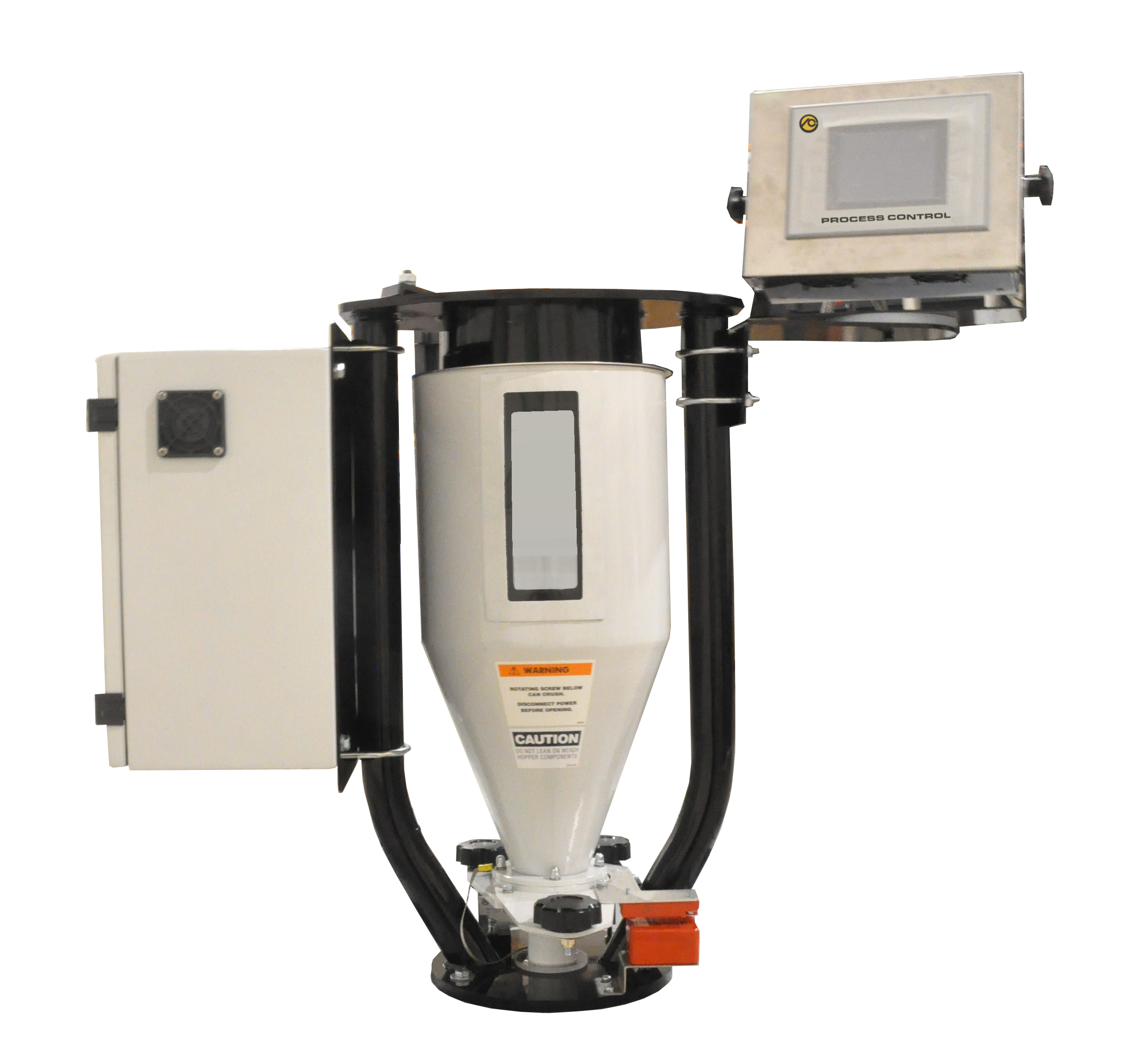
Control for X Series 2 Blenders
Process Control X Series 2 blenders monitor the extruder usage in order to follow the extruder rate and insure a consistent supply of material. In an extrusion control system, this extruder rate is used to adjust the screw speed by minute amounts to hold the overall throughput to the value entered in the blender operator station. Because the blender already has a powerful computer and equipment necessary to measure the extruder rate, adding extrusion control on a monoextrusion line with a Process Control X Series 2 blender is a very cost-effective addition. This feature can be easily retrofitted to existing installations with X Series 2 or B Series blenders.
X Series 2 blenders can also be easily integrated into coextrusion applications with extrusion control for controlling product layer ratios and total line throughput. On coextrusion applications the blender computer reports to a master EXB2 Series Operator Station, which also receives weight throughput reading from HG Series 2 Weigh Hoppers mounted on single-component extruders.

Check back next week for a brief introduction to the GRAVITROL® Extrusion Control Systems’ special features and products.
For this information and more on our GRAVITROL® Extrusion Control Systems, please click here to access our website, or send us an e-mail at sales@process-control.com.
This week’s entry would like to spotlight the X Series 2 Continuous Blender. The X Series 2 is designed to produce precise, homogeneous blends by weight and offers unsurpassed blend accuracy and blend homogeneity in a wide range of configurations to meet the needs of any application. For extruder throat-mounted applications, the X Series 2 blender comes equipped with an integral downcomer to preserve the blended material all the way to the extruder without demixing. For mezzanine or off-line mounting, the blender does not include the downcomer and is designed to work with a number of different options for storing the blended material prior to it’s use.
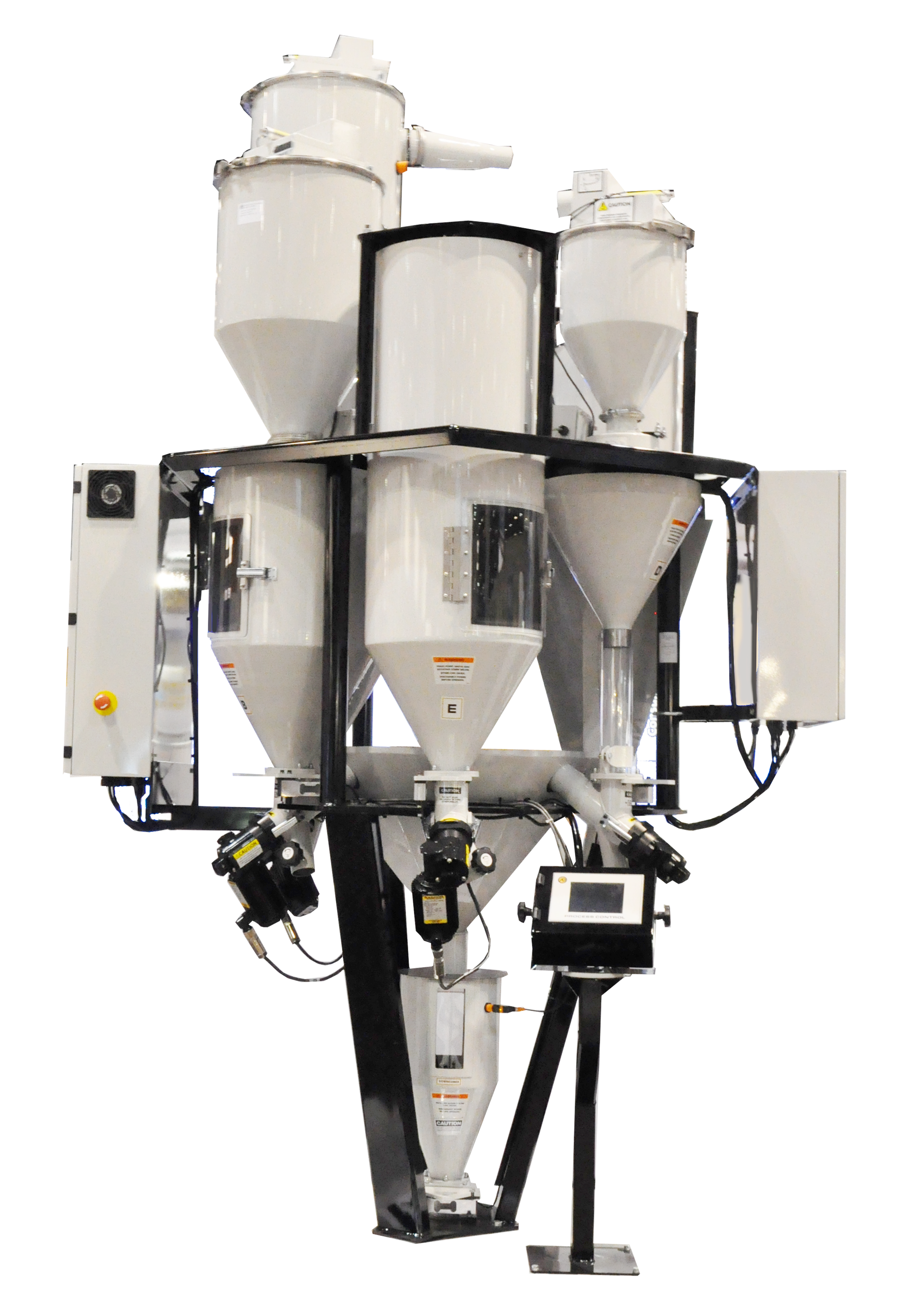
Mechanical Features
- Individual weighed ingredient hoppers with easy-to-use drains
- Interchangable metering units with quick disconnect
- Brushless DC gear motors with closed-loop control for precise ingredient measuring
- Integral loading platform for mounting vacuum receivers
- Designed for easy clean-out and quick change over
- Color touch screen operator interface with new “off-the-shelf” control
Control Features
- Blender monitors weight loss of each ingredient hopper for precise control of blend ratios.
- Weighing system resolution is 1:1,000,000 for maximum accuracy.
- Color touchscreen display for easy viewing of inventory and performance data.
- Storage for 400 blend recipes in battery-backed memory.
- Multiple alarm levels with visual display and contact closures.
Options
- Gravimetric Extrusion Control
- Steep-wall hoppers for regrind and other sluggish materials.
- Powder Feeder metering elements
- High temperature design
Be sure to check out our videos related to the use and care of the X Series 2 Continuous Blender, such as the Material Cleanout Procedure featured on this blog. Also be sure to check in with your Process Control Sales Representative for the latest upgrades for your PCC X Series 2 Continuous Blender!
For more information on the X Series 2, click here to visit our website, check out the literature, or contact us directly at sales@process-control.com.
Process Control Corporation is pleased to announce the release of the newly redesigned PF Series Powder Feeder. This new design is more robust than its predecessors, and allows for increased efficiency and lower maintenance. Special features include weephole for visual monitoring of the system.
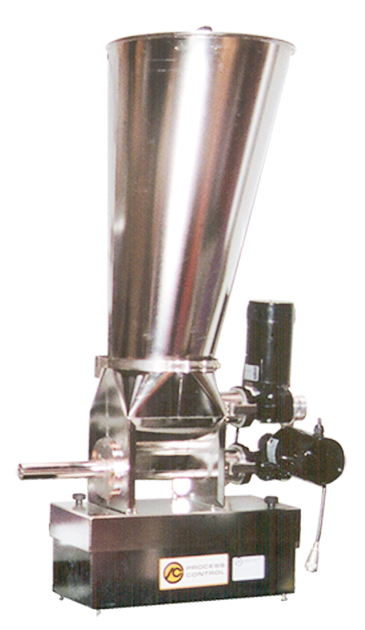
Carried over for the PF Series, this feeder offers operators unprecedented metering accuracy from ultra low rates up to 3000 pounds per hour.
Incorporated into the brushed stainless steel design is a unique round-to-trough feeding area which provides more consistent mass flow for better metering accuracy. The feeder is designed with a steep wall, removable hopper which features a dust-tight band clamp for easy mounting of hopper extensions and quick disassembly for clean out. The bottom trough design is optimized to provide maximum material exposure to the auger.
Separate drives for the agitator and metering auger allow appropriate agitation at all auger speeds. Metering augers are available at full pitch or 1/2 pitch configurations with helix diameters from 1/4in to 2-1/4in. The PF Series can be configured with controls for intermittent agitator operation, which is particularly useful when operating at very low rates. Additionally, this variable speed agitator permits thorough mixing in all areas of the metering section.
The unprecedented metering accuracy of the PF Series Powder feeder is enhanced by a proprietary filtering method which allows very accurate and consistent gravimetric metering in the presence of ambient vibration and electrical noise.
The feeder is available either as a stand alone or configured as an element on a gravimetric blender. Be sure to also check out the product spotlight on the XU Series 2 Continuous Gravimetric Powder Blender and watch how to put together the new PF Series Powder Feeder on PCC’s Youtube Channel.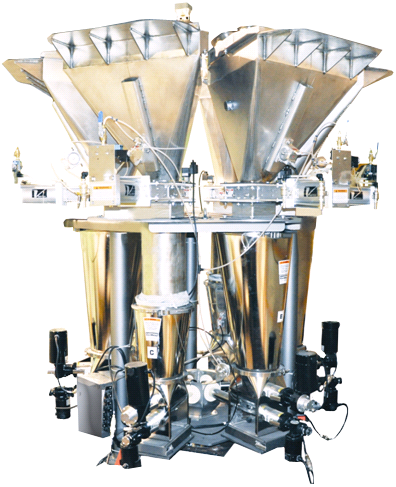
For more information on the PF Series Powder Feeder, please visit our website or contact us directly at sales@process-control.com.
Today’s blog entry will feature Process Control’s X2U Series Continuous Gravimetric Powder Blender. The X2U offers unsurpassed blend accuracy and blend homogeneity in a wide range of configurations to meet the needs of any application incorporating the PF Series powder feeders. It allows gravimetric blending of non-free-flowing powder materials with free-flowing powder and pellet materials at unprecedented metering and mixing accuracy.
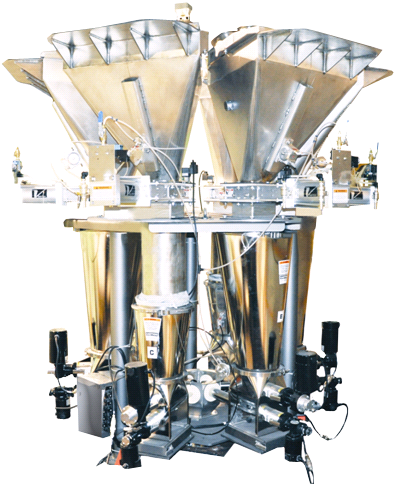
The powder feeders allow rates as low as 0.2PPH and as high as 3,000PPH. Metering augers are available in full pitch or 1/2 pitch configurations with helix diameters from 1/4 inch to 2-1/4 inches.
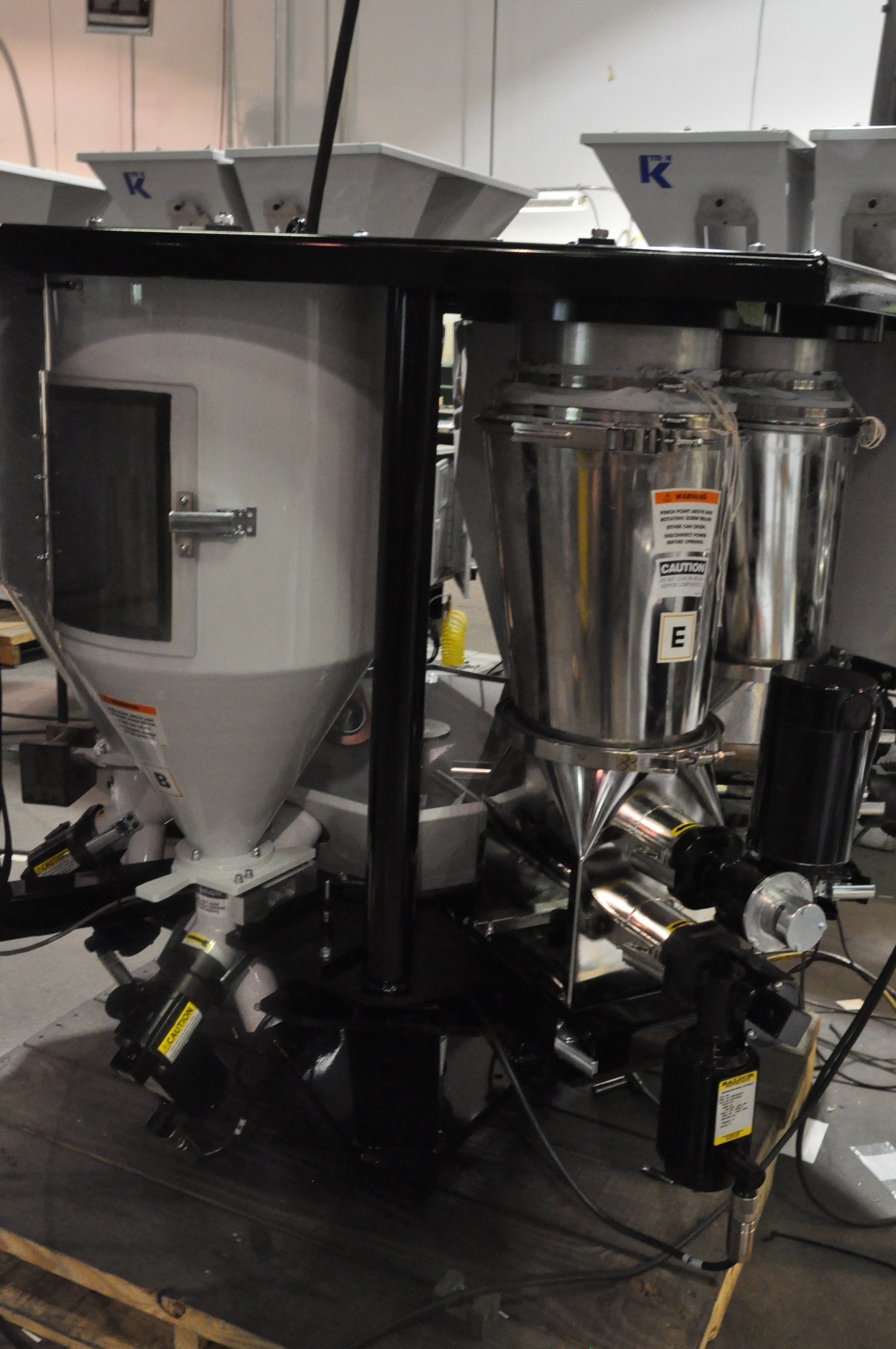
9 element Continuous Blender equipped with 3 powder feeders, 2 pellet, and 3 regrind hoppers
Incorporated into the electro-polished stainless steel design is a patented round-to-trough feeding area which provides more consistent mass flow for better metering accuracy. The feeder is designed with a steep wall, removable hopper which features a dust-tight band clamp for easy mounting of hopper extensions and quick disassembly for clean out. The bottom trough design is optimized to provide maximum material exposure to the auger.
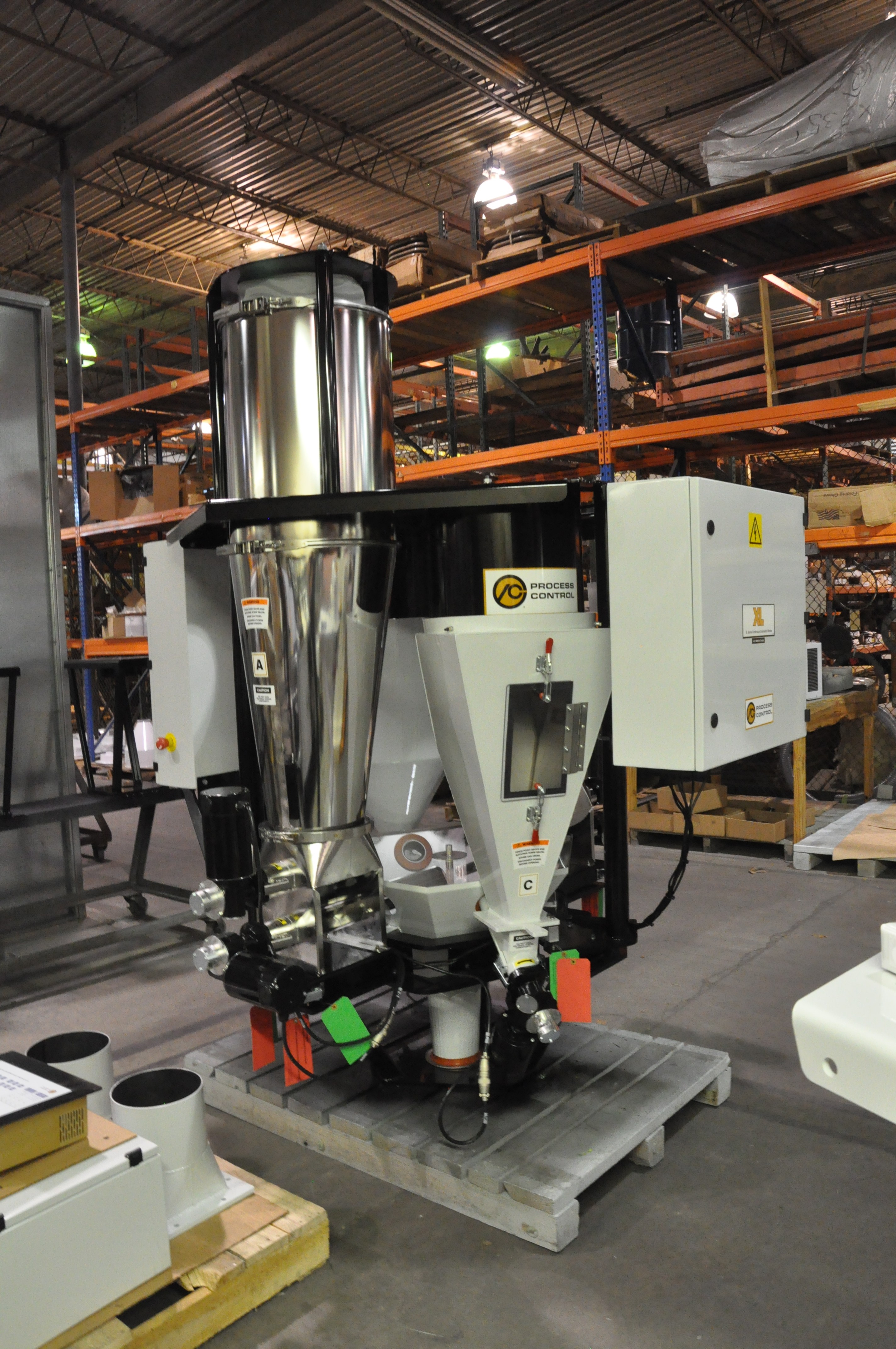
Another configuration with a larger powder feeder
For more information on the X2U, please visit our website or download the spec sheet. Be sure to also check out Process Control’s PF series powder feeders.
The recovery of scrap generated during the production of blown film, cast film, tape and extrusion coating processes is a key element in reducing manufacturing costs. The Automatic Scrap Recycling system – or ASR®, for short – can recycle trim scrap and off-spec roll scrap in-line and turn your scrap back into profit without the expense of repelletizing.
A complete ASR system consists of several components, and for the next three weeks Process Control is pleased to detail this patented Automatic Scrap Recycling system. The three components covered will include the following: The RMX Series Refeed Machine, the IN Series Trim Removal Inducer, and the GF Series Film Scrap Grinder.
This week, PCC would like to highlight the features of our GF Series Film Grinder for automatic scrap recycling applications.
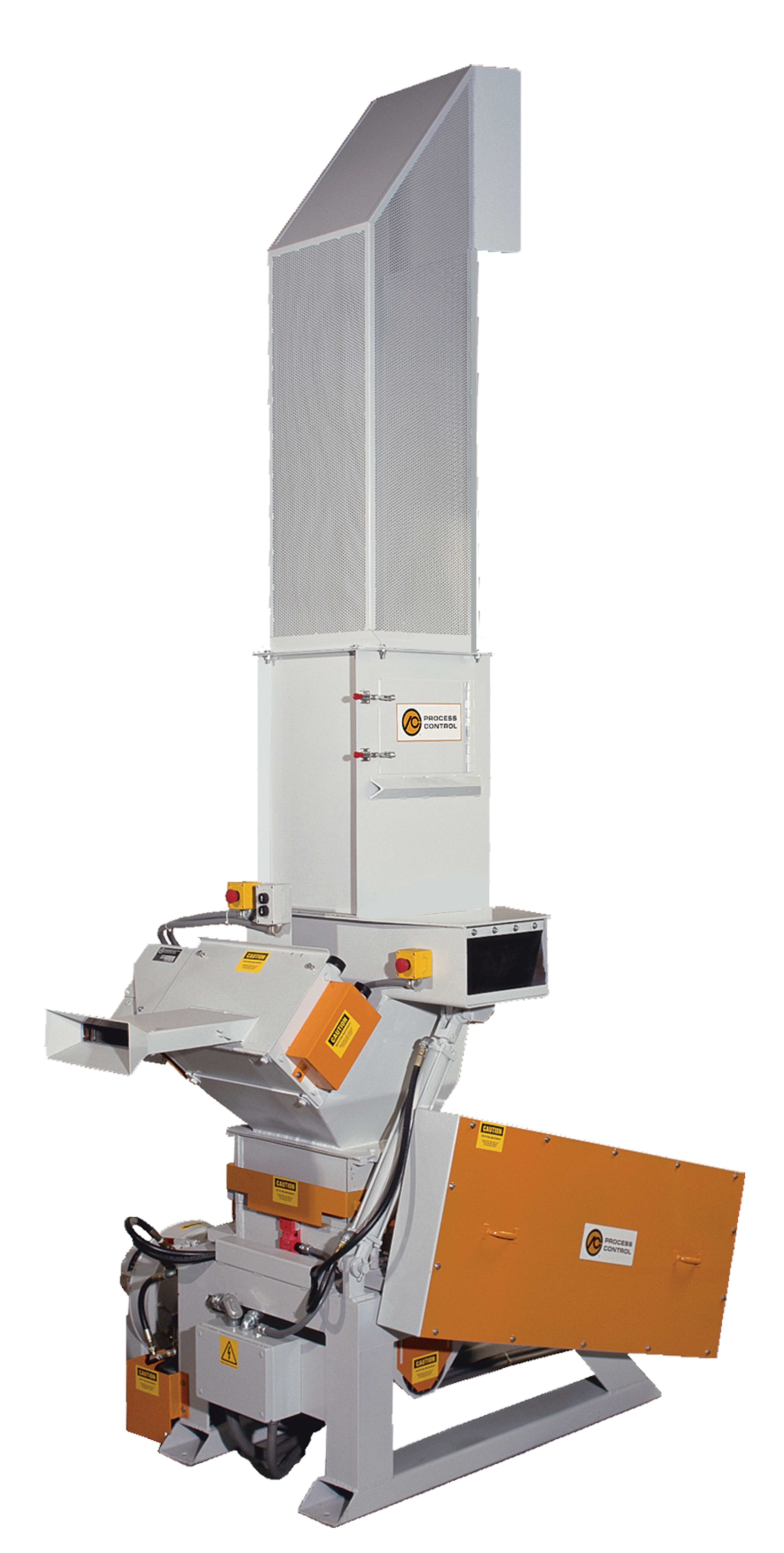
The GF Series grinders from PCC are used as part of an ASR Automatic Scrap Recycling system for in-line recycling of production film scrap. GF grinders are designed to provide efficient, uniform grinding o film scrap. There are four cutting chamber sizes available along with different horsepower motors to accurately match the grinder to the scrap rate. Grinders are available in configurations that accept edge and bleed trims, roll scrap, and loose scrap.

Standard carbide-coated knives are employed in the system, increasing the time between sharpening. The rotor knives approach the stationary bed knife, or knives, at a steep angle to ensure a clean scissor cut. This technique is used for maximum bulk-density and flow of ground scrap. The open rotor design improves airflow for cooling, permitting the highest possible throughput.
Click here for more information on the GF Series Film Grinder.
For more information on the ASR® Automatic Scrap Recycling System and Process Control’s other products and upgrades , please visit our website or contact us directly at sales@process-control.com.
The recovery of scrap generated during the production of blown film, cast film, tape and extrusion coating processes is a key element in reducing manufacturing costs. The Automatic Scrap Recycling system – or ASR®, for short – can recycle trim scrap and off-spec roll scrap in-line and turn your scrap back into profit without the expense of repelletizing.
A complete ASR system consists of several components, and for the next three weeks Process Control is pleased to detail this patented Automatic Scrap Recycling system. The three components covered will include the following: The RMX Series Refeed Machine, the IN Series Trim Removal Inducer, and the GF Series Film Scrap Grinder.
This week, PCC will be featuring the IN Series Trim Removal Inducer.
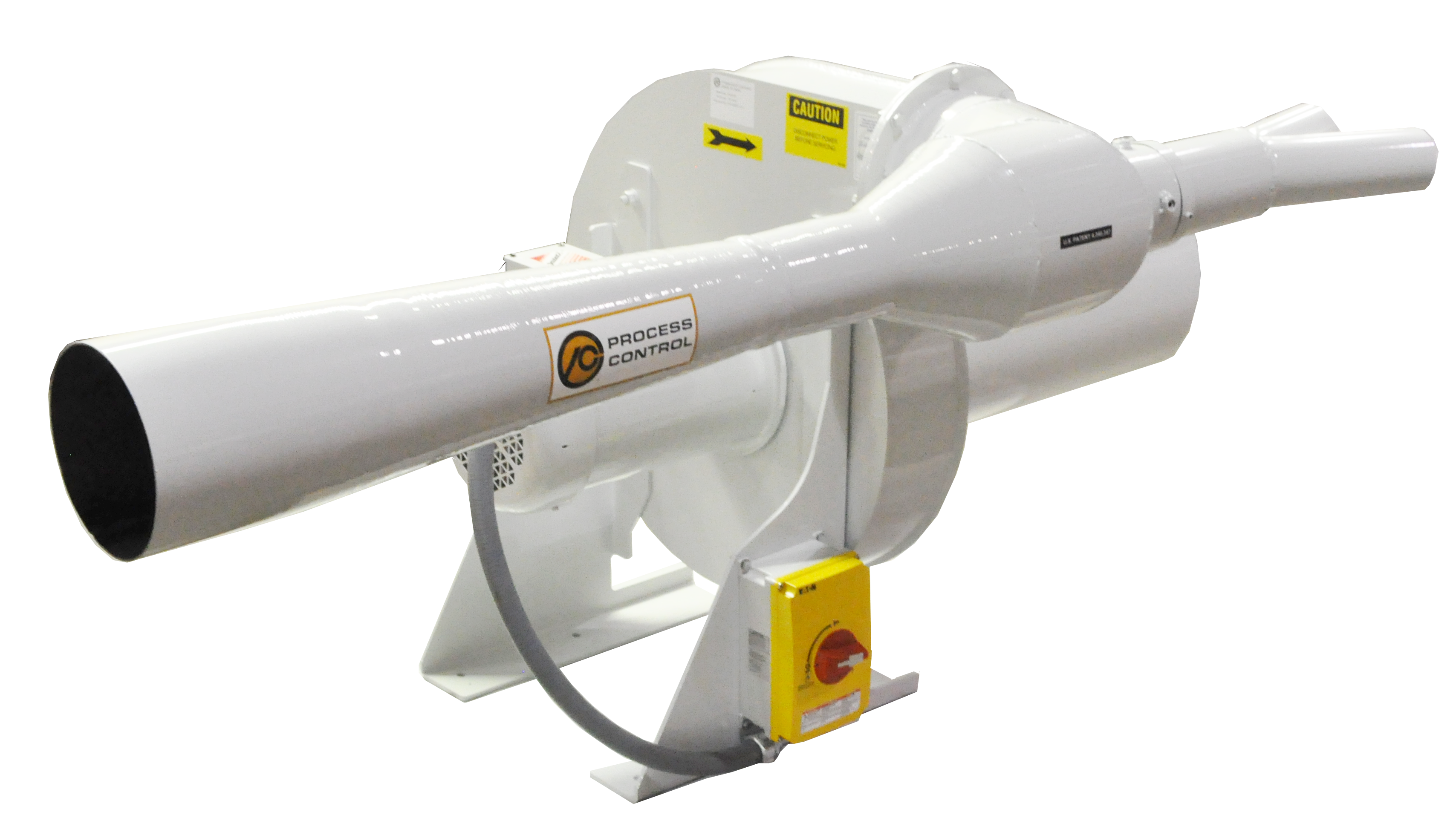
Process Control’s IN Series Inducers are designed to pick up and convey edge and/or bleed trims generated in the production of plastic film or other thin-gauge products such as foam, tape, paper or foil. These continuous trims are picked up by suction, conveyed into the inducer’s venturi section and blown to a destination such as a Process Control film grinder or a waste container.
Process Control inducer manifolds are designed to insure that the air velocity at the pickup point is maintained so that the trims do not wrap around the cutters. The IN Series inducers feature an adjustable venturi to allow you to tune the inducer for peak performance with your installation. IN Series inducers have a higher induced air to primary air ratio than conventional trim removal systems, providing excellent pickup and conveying performance.
IN Series inducers are designed to adapt easily to the installation requirements of your extrusion lines. The unit is shipped with its fan in a top-horizontal arrangement, but can be easily rotated in 90° increments to provide the required fan/venturi orientation. The fan may also be mounted remotely from the venturi using additional tubing.
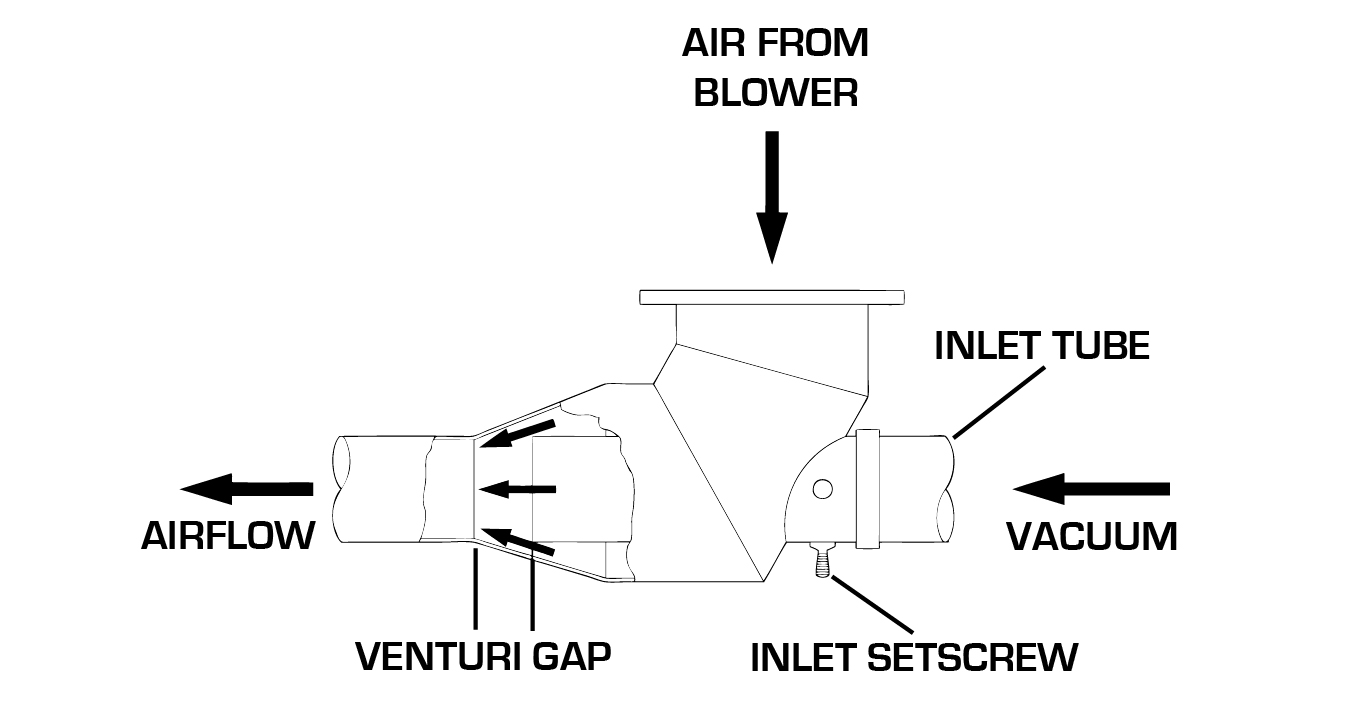
Process Control’s patented venturi design uses the same principle used to create lift with an aircraft wing. The venturi design is far more efficient than the more commonly used cyclonic design, resulting in more suction and far greater air flow per fan CFM. This efficiency reduces the required horsepower, which results in lower energy costs, reduced noise and easier separation of the trim from the conveying air at the grinder.
Read more about it here.
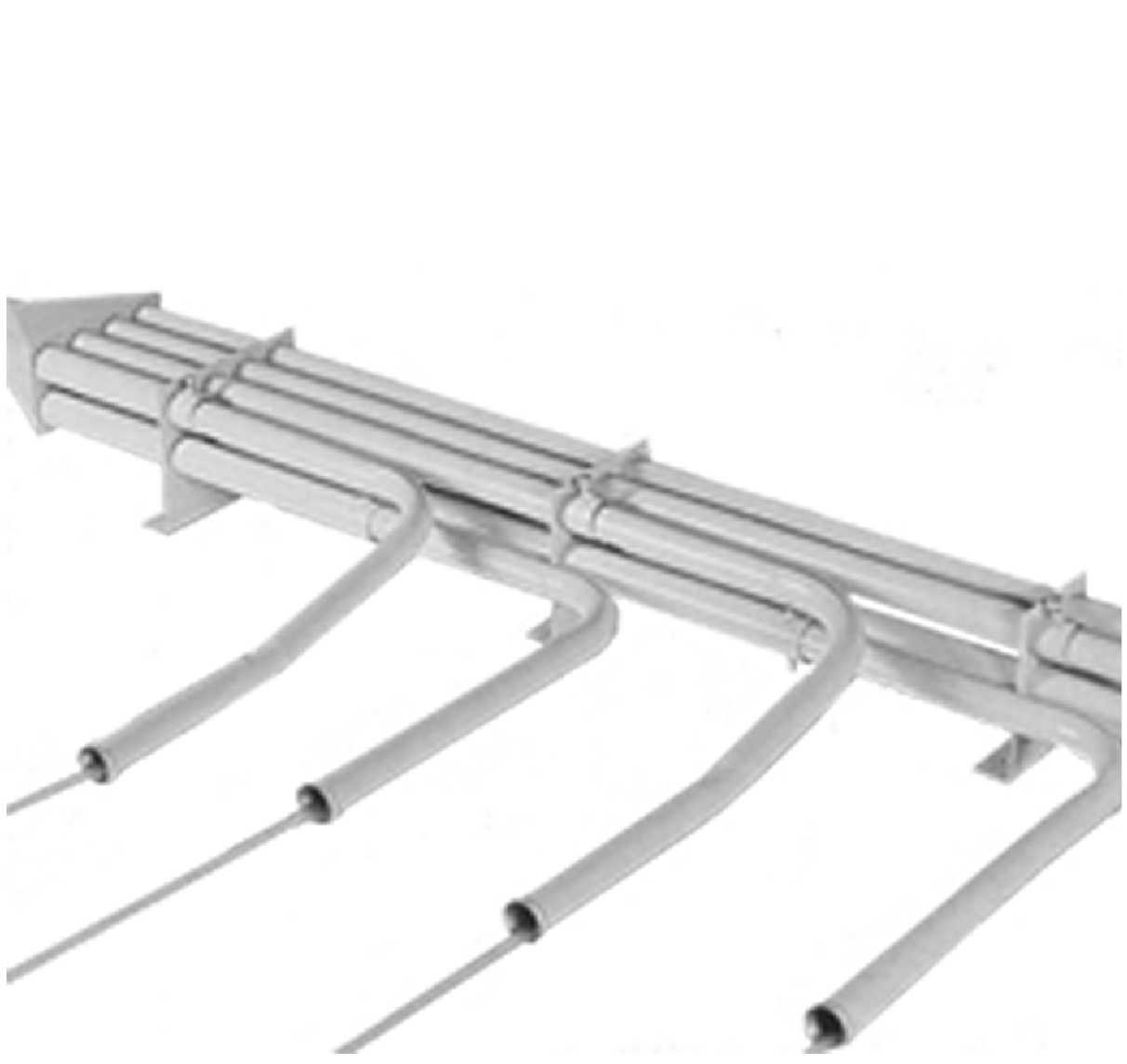
Click here for more information on the IN Series Trim Removal Inducer.
For more information on the ASR® Automatic Scrap Recycling System and Process Control’s other products and upgrades , please visit our website or contact us directly at sales@process-control.com.
The recovery of scrap generated during the production of blown film, cast film, tape and extrusion coating processes is a key element in reducing manufacturing costs. The Automatic Scrap Recycling system – or ASR®, for short – can recycle trim scrap and off-spec roll scrap in-line and turn your scrap back into profit without the expense of repelletizing.
A complete ASR system consists of several components, and for the next three weeks Process Control is pleased to detail this patented Automatic Scrap Recycling system. The three components covered will include the following: The RMX Series Refeed Machine, the IN Series Trim Removal Inducer, and the GF Series Film Scrap Grinder.
Today PCC is happy to show off its RMX Series Refeed Machine. This machine is specifically designed for use with Gravitrol® Gravimetric Extrusion Control Systems. The compact size also makes the RMX Series suitable for applications with headroom restrictions without sacrificing the performance that has made the ASR® Refeed Machine popular for film applications. The unique, double-compartment RMX Series Refeed Machine operates with a variable-speed auger/bridge-breaker assembly to compact and meter ground scrap from the inner hopper to the throat of the production extruder. The outer compartment contains virgin material which is gravity-fed to the throat. The virgin material completely surrounds the ground scrap as it enters the extruder. The extruder screw receives a consistent column of compacted ground scrap surrounded by virgin material.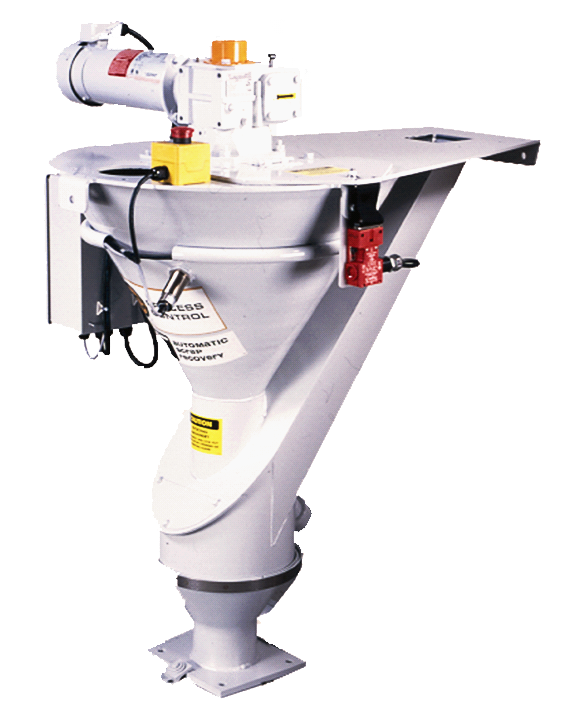
This method provides consistent operation without extruder surging or starvation. With the standard extruder follower circuit, the refeed machine will increase or decrease the scrap rate in proportion to the extruder speed. This holds scrap percentage constant without additional operator attention. The touch screen operator panel with smart HMI provides full control and configuration of the drive system with minimal setup. The roll feeder and refeed status may be monitored from a single screen.
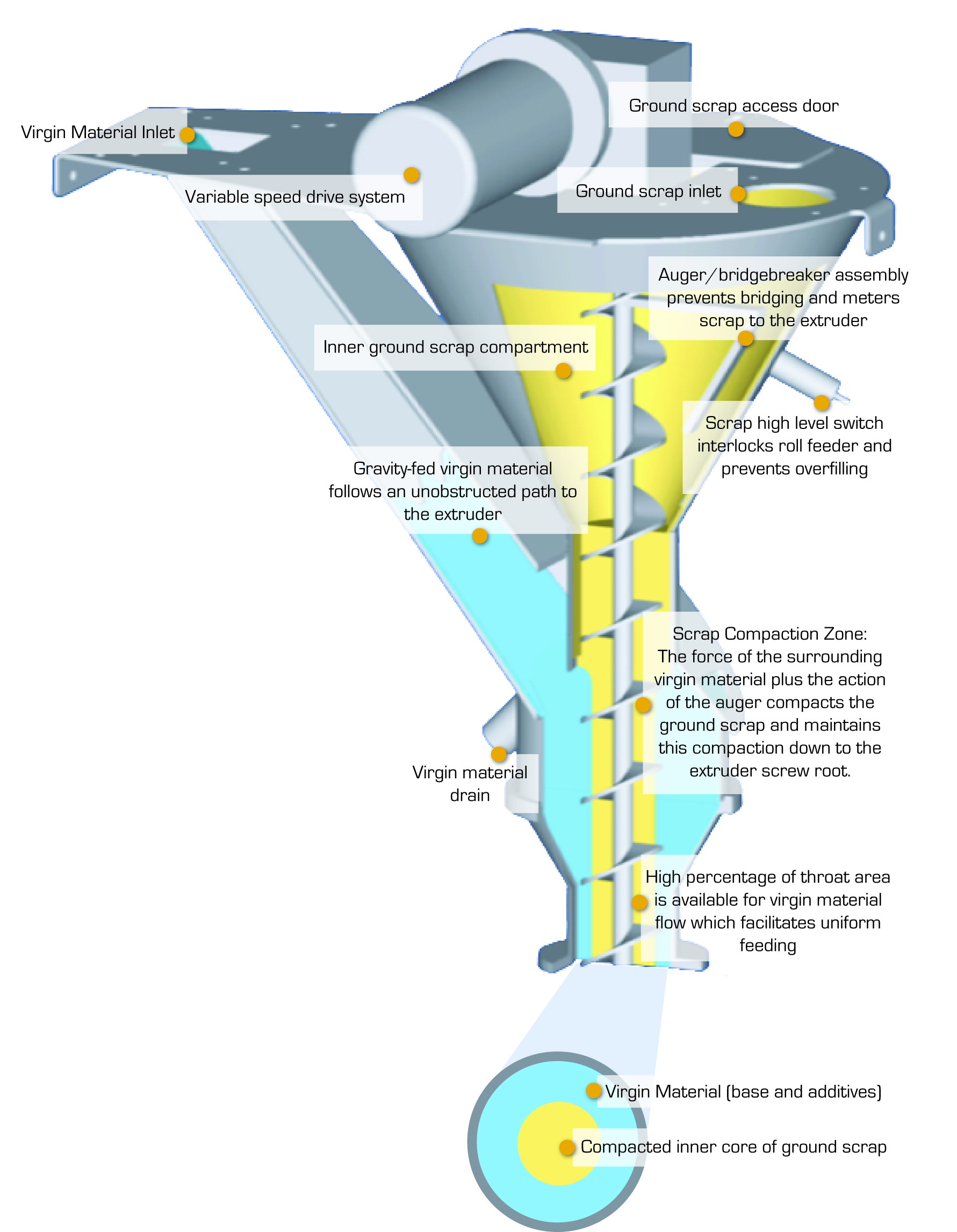
Click here for more information on the RMX Series Refeed Machine
Be sure to also read up on the RMX Series’ new Operator Control Panel.
For more information on the ASR® Automatic Scrap Recycling System and Process Control’s other products and upgrades , please visit our website or contact us directly at sales@process-control.com.
In today’s entry, we would like to highlight the features of our integrated real-time trending, material management, and monitoring program called Blend Manager.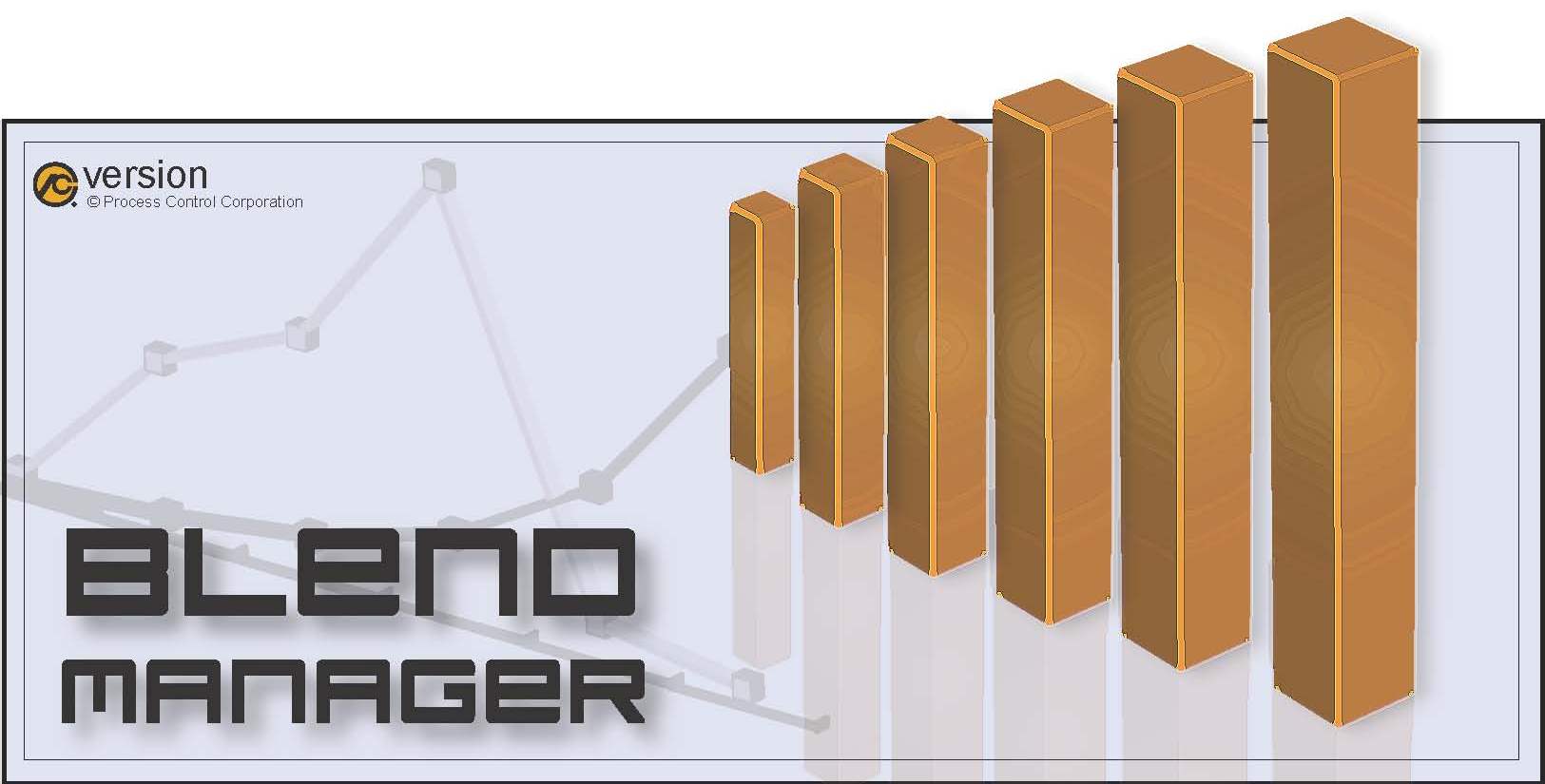
Blender Manager has integrated real-time trending, historical trend data, material management and monitoring in a single package. A simple, easy to use wizard guides the user through setup of program settings. The program itself has been thoroughly designed for reliability and ease of use. All settings and data are stored in SQL databases. Communications with Process Control’s equipment is via Modbus TCP. The driver is integrated into the software and requires no complicated setup. Here are some more of the program’s features:
Trending and Historical Data
• Both real-time and historical trend data can be zoomed and/or scaled on both X and Y axis.
• Move between viewing real-time and historical trend data with a simple tabbed interface.
• Real-Time data is seamlessly stored to a historical SQL database.
Material Management
• Material management report generation can be generated based on a defined shift schedule or on the fly as needed.
• Material management reports can be sent to a printer or saved as a PDF.
Monitoring
• Monitor critical equipment parameters on a single window.
For more information on Blend Manager, please download the product cut sheet or contact us directly at sales@process-control.com.
Process Control is pleased to present an all new RMX Series Refeed Machine Operator Panel available for ASR® Automatic Scrap Recycling. Hardware includes an HMI/PLC combo with Digital and Analog I/O, Modbus, & Ethernet. A variety of AC drive brands are available. The RMX Operator Panel can operate as a standalone system, or it can integrate with PCC (and most other) grinder and roll feed systems. It also comes with the ability to integrate with supervisory systems via Ethernet.
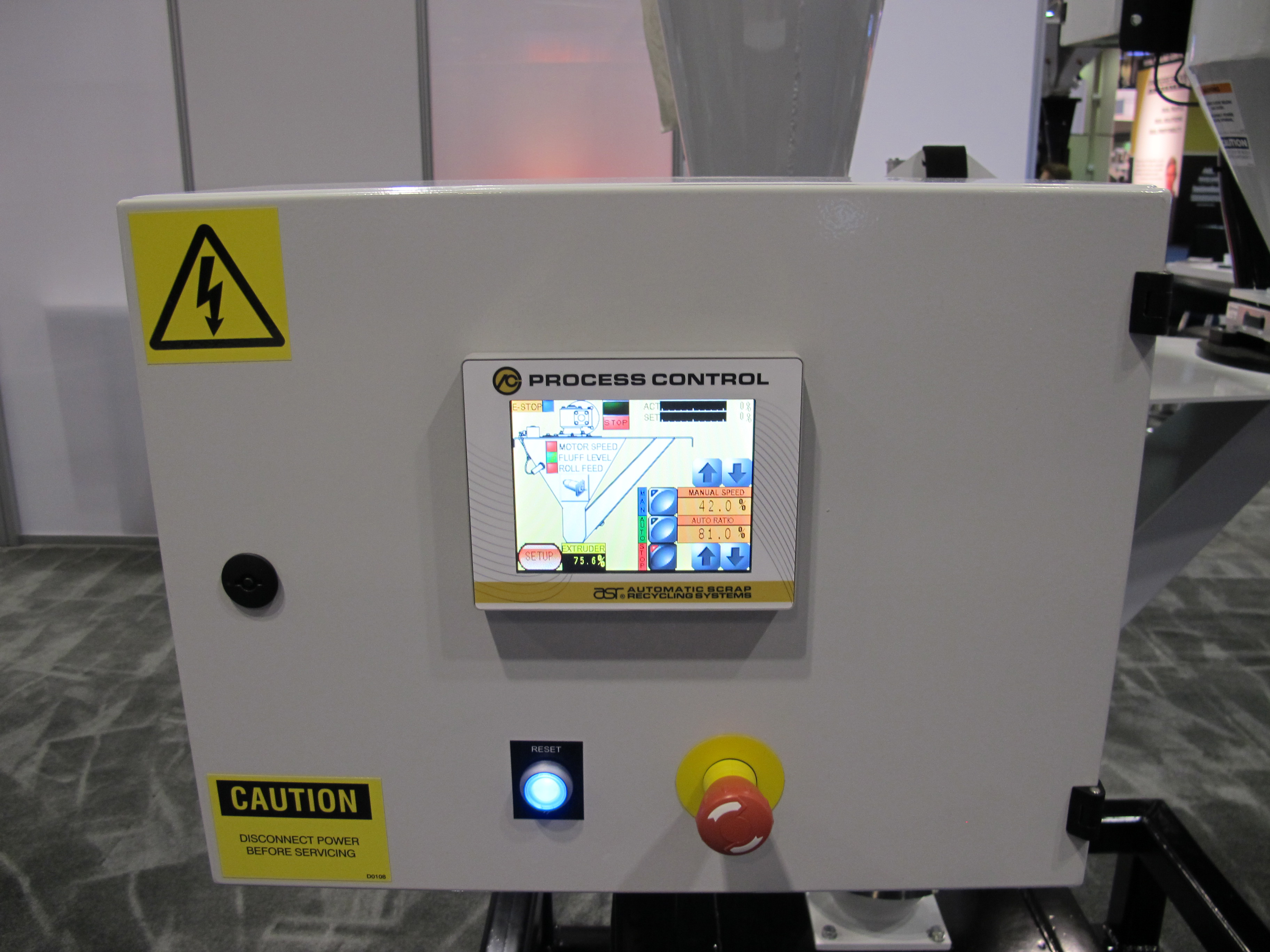
Operation modes for this panel include an auto, manual, and maintenance mode. Auto allows the user to set the speed ratio, and the PLC calculates the correct refeed speed based on extruder speed. Manual allows for direct speed entry, and maintenance provides forward and reverse job for cleanout and inspection. Advanced setup options for this panel include an ad adjustable rate/frequency curve for special materials and a simplified interface. This means you can hide the options you don’t need!

Most importantly, the RMX Series Refeed Machine Operator Panel provides a number of advantages. Smart HMI provides full control and configuration of drive system while competitors require in-panel adjustments. Monitor roll feeder and refeed status are read from a single screen, making the system easier and faster to read, plus system alarms are provided through a pop-up alert so it’s easy to find. Plus there is minimal drive setup because most of the parameters are set onscreen, and an easy switchover to various drive brands.
For more information on the ASR® Automatic Scrap Recycling System and Process Control’s other products and upgrades , please visit our website or contact us directly at sales@process-control.com.

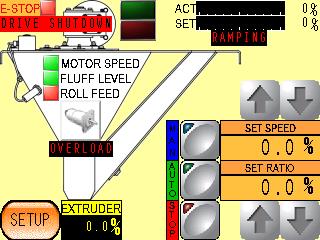
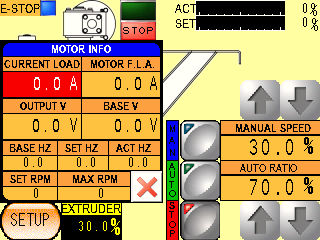
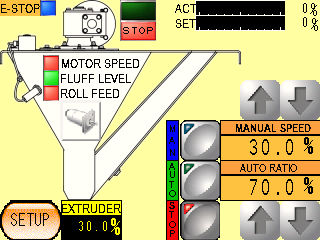
Today’s blog entry will feature Process Control’s PF Series Powder Feeder. The PF Series offers operators unprecedented metering accuracy from ultra low rates up to 3000 pounds per hour.

PF Series Powder Feeder
Incorporated into the brushed stainless steel design is a unique round-to-trough feeding area which provides more consistent mass flow for better metering accuracy. The feeder is designed with a steep wall, removable hopper which features a dust-tight band clamp for easy mounting of hopper extensions and quick disassembly for clean out. The bottom trough design is optimized to provide maximum material exposure to the auger.

Guardian Series 2 Batch Blender with Powder Feeder
Separate drives for the agitator and metering auger allow appropriate agitation at all auger speeds. Metering augers are available at full pitch or 1/2 pitch configurations with helix diameters from 1/4in to 2-1/4in. The PF Series can be configured with controls for intermittent agitator operation, which is particularly useful when operating at very low rates. Additionally, this variable speed agitator permits thorough mixing in all areas of the metering section.
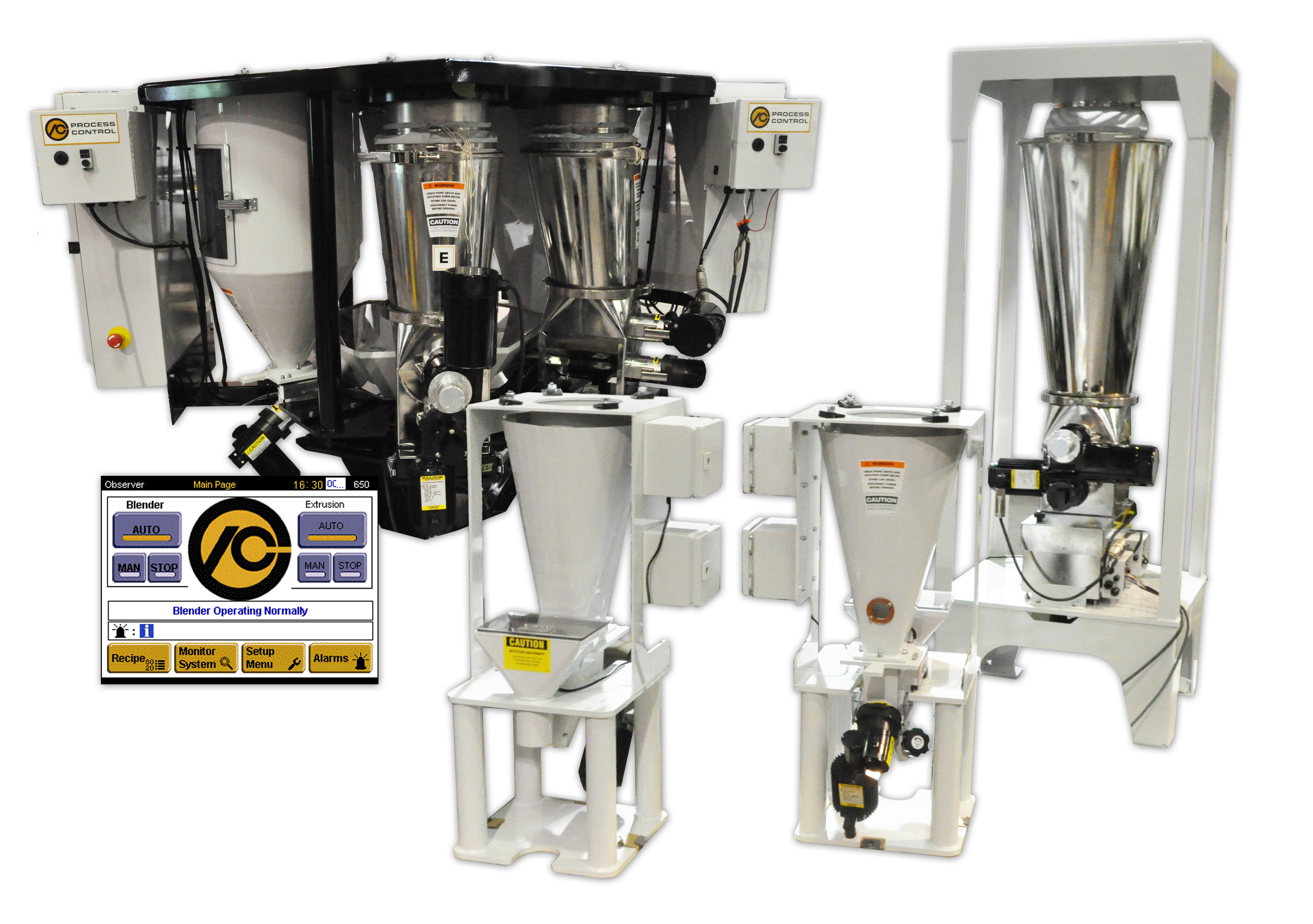
Continuous Blender Powder System
The unprecedented metering accuracy of the PF Series Powder feeder is enhanced by a proprietary filtering method which allows very accurate and consistent gravimetric metering in the presence of ambient vibration and electrical noise.
The feeder is available either as a stand alone or configured as an element on a gravimetric blender. For more information on the PF Series Powder Feeder, please visit our website or contact us directly at sales@process-control.com.